In the fast-paced world of manufacturing, time is money, and resources are precious. Enter virtual prototyping, a revolutionary approach that’s turning the industry on its head. Gone are the days when creating a new product meant endless cycles of physical prototypes, each iteration eating up time and materials. Today, manufacturers are embracing 3D technology to streamline product development in ways that were once the stuff of science fiction.
From Concept to Digital Reality
Imagine being able to test, tweak, and perfect a product before a single physical component is produced. That’s the magic of virtual prototyping. Using sophisticated 3D modeling software, engineers and designers can create highly detailed digital representations of their products. These virtual models aren’t just pretty pictures on a screen; they’re powerful tools that simulate real-world physics, materials, and conditions.
Let’s take a journey through a typical product development process using virtual prototyping. It all starts with a concept. Instead of sketching on paper or building rough physical models, designers jump straight into 3D modeling software. They craft every curve, every joint, and every component in exquisite detail. The beauty of this approach? Changes can be made with a few clicks, not hours of rework.
Testing in the Virtual Realm
As the virtual model takes shape, engineers can start putting it through its paces. Want to know how that new chair design will hold up under different weights? No need to build it and sit on it repeatedly. Virtual stress tests can simulate thousands of sitting scenarios in minutes. Curious about how your new smartphone will fare if dropped? A digital drop test can provide insights without sacrificing a single physical prototype.
Collaboration and Customization Reimagined
But the benefits of virtual prototyping go far beyond simple testing. One of the most exciting applications is in collaborative design. In the past, if teams from different departments or even different countries wanted to work on a product together, they’d need to ship physical prototypes back and forth. Now, they can all work on the same virtual model in real-time, no matter where they are in the world. This not only speeds up the design process but also fosters innovation as diverse perspectives can be integrated more easily.
Virtual prototyping is also a godsend for customization. In an era where consumers increasingly want products tailored to their specific needs, manufacturers can use 3D technology to quickly mock up and test variations without the cost of producing multiple physical versions. This opens up new possibilities for mass customization that were previously impractical or too expensive.
The Economics of Virtual Prototyping
The cost savings of virtual prototyping are staggering. Traditional product development often involved creating multiple physical prototypes, each potentially costing thousands or even millions of dollars. With virtual prototyping, the bulk of testing and refinement happens digitally, dramatically reducing material waste and cutting down on the number of physical prototypes needed. This not only saves money but also aligns with growing environmental concerns in manufacturing.
But it’s not just about savings; it’s about speed to market. In competitive industries, being first can make all the difference. Virtual prototyping allows companies to iterate faster, solve problems quicker, and get products to market in record time. What might have taken months or years can now be accomplished in weeks or months.
Cross-Industry Applications
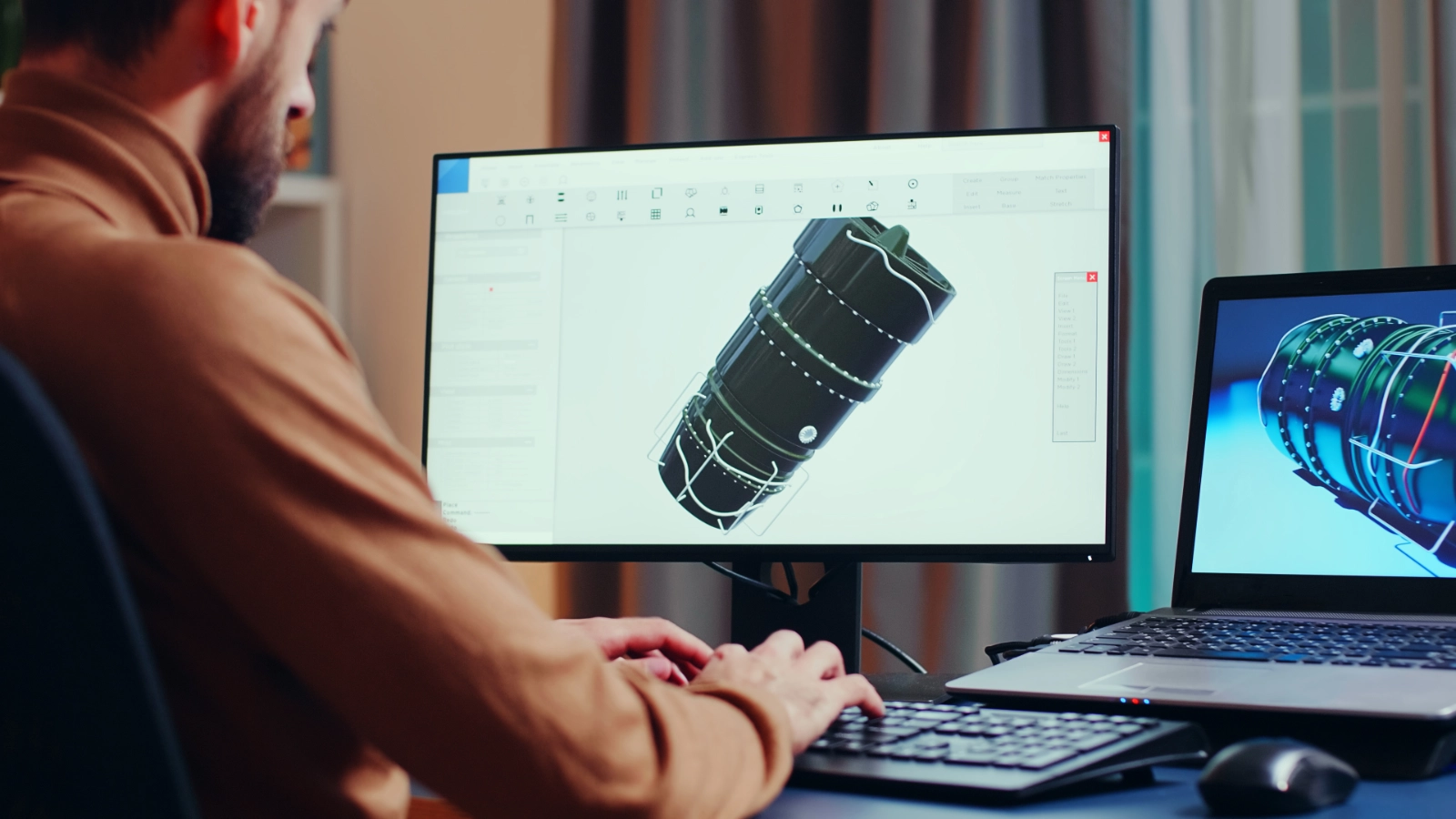
The applications of virtual prototyping span across industries. In automotive manufacturing, entire vehicles can be designed and tested virtually, from aerodynamics to crash safety. Aerospace companies use it to simulate complex systems and optimize aircraft designs long before any metal is cut. Even in fields like medicine, virtual prototyping is making waves, allowing for the design of custom prosthetics and medical devices tailored to individual patients.
The Future of Virtual Prototyping
As virtual prototyping technology advances, we’re seeing the integration of other cutting-edge technologies. Virtual and augmented reality, for instance, are taking virtual prototyping to new levels of immersion. Designers can now walk around their creations in virtual space, getting a feel for the product that goes beyond what’s possible on a flat screen. AI and machine learning are being employed to optimize designs automatically, suggesting improvements based on vast datasets of previous products and real-world performance data.
A Paradigm Shift in Manufacturing
The shift to virtual prototyping represents more than just a change in tools; it’s a fundamental shift in how we approach product development. It’s about thinking digitally from the outset, about embracing simulation and data-driven design decisions. For manufacturers willing to invest in the technology and expertise, virtual prototyping offers a competitive edge that’s hard to beat.
As we look to the future, the line between virtual and physical prototyping will likely blur even further. With advancements in 3D printing, we may see hybrid approaches where virtual designs can be quickly realized as physical objects for final testing or customer feedback. The possibilities are as limitless as our imagination.
Virtual prototyping is more than just a trend; it’s the future of manufacturing. By leveraging 3D technology to streamline product development, manufacturers are not just saving time and resources – they’re unleashing creativity, fostering collaboration, and pushing the boundaries of what’s possible. In a world that demands innovation at breakneck speed, virtual prototyping isn’t just an option; it’s a necessity for staying ahead of the curve.